Die Bentley Motors Ltd. im britischen Crewe wurde häufig als "größter Showroom der Welt" beschrieben. Seit Jahren kommen gegenwärtige und zukünftige Bentley-Besitzer aus der ganzen Welt hierher, um zu erleben, wie die sorgfältig von Hand gefertigten Autos nach und nach Gestalt annehmen, und um die einmalige Gelegenheit wahrzunehmen, mit den Leuten zu sprechen, die diese Bentleys herstellen.
Die Einführung des Continental GT stellt das Werk in Crewe jedoch vor eine Reihe neuer Herausforderungen. Mit einem W12-Motor und Allradantrieb zählt der Continental GT derzeit zu den komplexesten und fortschrittlichsten Autos auf der Straße. Es war keine leichte Aufgabe für das Fertigungsteam in Crewe, die Produktion dieses außergewöhnlichen, neuen "British Grand Tourers" in wesentlich höherer Stückzahl nach höchsten Benchmark Qualitätskriterien sicherzustellen, ohne dabei die menschliche Komponente, die handwerklichen Fähigkeiten der Mitarbeiter und die Interaktion mit dem Kunden aus dem Blick zu verlieren, die seit jeher so wesentliche Merkmale der Marke Bentley sind.
Das Ergebnis aller Investitionen ist nicht nur eine neue Fertigungsanlage, sondern vielmehr ein ganz neues Werk. Jede Komponente des Herstellungsprozesses ist in enger Abstimmung mit den Teamchefs der 1200 Crewe-Mitarbeiter, die an der Bentley-Herstellung beteiligt sind, neu geschaffen worden. Als Teil des Volkswagenkonzerns profitierte Bentley Motors von einem mit 800 Millionen Euro dotierten Investitionsprogramm, wobei 91 Millionen Euro direkt in das Werk Crewe flossen.
Handgefertigte Bentley Motoren
Seit den Anfangstagen von Bentley in Cricklewood unter den wachsamen Augen eines Walter Owen ("W.O.") Bentley war die Entwicklung und der Bau des Motors immer das Herzstück des Wagens, und der Continental GT macht in dieser Beziehung keine Ausnahme. In den Zeiten von W.O. wurden im Werk nur Motoren und Fahrgestelle produziert, während die Aufbauten von spezialisierten Karosserieherstellern angefertigt wurden; heute entsteht die Karosserie für den Continental GT in den Produktionsstätten der Volkswagen-Gruppe in Mosel, wodurch sich der Vorteil von spürbaren Kosteneinsparungen ergibt. Aber der Bentley Twin-Turbo-W12-Motor für den Continental GT wird von Grund auf in Crewe montiert.
Das Kurbelgehäuse des Motors und eine große Zahl seiner Komponenten wird auf einem automatischen Fahrschemel zusammengesetzt, der über eine eigene Stromversorgung verfügt und mit einem Lasersteuerungssystem ausgestattet ist, das auf den Boden gezeichneten schwarzen Linien folgt. Der Fahrschemel "besucht" jeden der 16 Montageplätze in einer festgelegten Folge und bleibt genau 17 Minuten an jedem Platz. Somit dauert es viereinhalb Stunden, um einen Bentley-Motor herzustellen, wobei die Gesamtfertigungsdauer einschließlich der Testphase 15 Stunden / Einheit beträgt.
Jeder Motor wird von Hand zusammengesetzt. Erfahrener Techniker leisten hier Präzisionsarbeit und montieren die exakt aufeinander abgestimmten Teile: Kurbelwellenlager, Kurbelgehäuse und Pleuellager, Kurbelwelle und Kolben.
Mit dem Fahrschemel verbunden sind elektrische Werkzeuge, die Verschlussmuttern und Bolzen festziehen. Während jeder Bolzen nacheinander vom Mechaniker festgezogen wird, informieren die elektrischen Maschinen ein Überwachungssystem, dass das korrekte Drehmoment erreicht wurde. Es ist unmöglich, eine Schraube "zu verpassen" oder sie nicht bis zum richtigen Drehmoment anzuziehen - bevor die Aufgabe erfüllt nicht ist, bewegt sich der Schemel nicht zur nächsten Station.
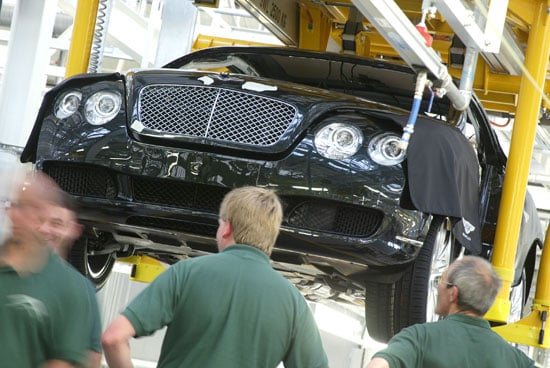
Jeder Continental GT-Motor wird zunächst einem Kalt-Test unterzogen, um zu prüfen, ob alles in Ordnung ist, bevor er an die Testanlage angeschlossen und zum ersten Mal gestartet wird. Wenn die Produktion angefahren ist, wird jeder Motor mindestens 2 Stunden auf dem Prüfstand getestet, wobei 10 Prozent der produzierten Motoren bis zu 48 Stunden unter Vollgas laufen, um den Fertigungsprozess einer kontinuierlichen Kontrolle zu unterziehen.
Produktionslinie: Von der Rohkarosserie zur "Hochzeit"
Während der Continental GT den Produktionsvorgang und die einzelnen Arbeitsstationen durchläuft und seine Bleche durch maßgeschneiderte Hüllen geschützt sind, die das berühmte geflügelte 'B'-Emblem von Bentley tragen, nimmt er nach und nach die Gestalt eines fertigen Bentleys an. Im Chassis-1-Bereich werden Elektrik-, Hydraulik-, Licht- und Klima-Systeme (Heizung, Lüftung und Klimaanlage) in die Rohkarosserie eingebaut. Von dort aus geht die Karosserie zur "Hochzeit", wo sie mit dem Motor, dem Fahrwerk und die Rädernaben "vermählt" und erkennbar zu einem Bentley Continental GT wird.
Holz - neue Techniken, Unterstützen das traditionellen Handwerks
Die ungebleichten edlen Furnierhölzer für Armaturenbrett, Konsole und Seitenverblendungen tragen wesentlich zum Charakter der Marke Bentley bei. Die Erfahrung mit dem Holzhandwerk, auf die man in Crewe zurückblicken kann, ist einzigartig in der Welt der Automobilproduktion.
Natürlich verarbeitet man in der Bentley-Holzwerkstatt nur die besten und von Hand ausgesuchten Furniere, aber zu ihrer Verarbeitung wendet man moderne Technik an, schon um Verschnitt zu vermeiden und die Qualität zu optimieren. Laser-Schneidegeräte, die bis auf 0,25 mm genau arbeiten, bringen die Furnierblätter in Form (Bentley besteht auf Furnieren, die 0,6 mm dick sind, obwohl die Industrienorm nur 0,4 mm vorgibt).
Die Holzverkleidung des Armaturenbretts hat sich stets dadurch ausgezeichnet, dass die Furniere ein symmetrisches Muster hatten und eine Seite spiegelverkehrt der anderen entsprach. Dies ist nur möglich, wenn zwei nebeneinanderliegende, hauchdünne Furnierblätter aus dem selben Baum verwendet werden. Der Continental GT ist keine Ausnahme, und die beiden achsensymmetrischen Furnierblätter sind am Ende mit einer zickzackförmigen Naht zusammengesetzt.
Zwischen der Trägerschicht und dem Edelholzfurnier wird ein Sandwich aus zwei quergefaserten Traghölzern sowie drei dazwischen liegenden Papierklebeblättern eingelegt, wobei das Grundblatt aus Mylar auf dem Trägermaterial haftet und das Deckblatt aus edlem Furnierholz den Abschluss bildet. Dies wird vier Minuten bei 135°C gepresst und verbunden, bevor die Oberfläche von Hand geschliffen wird. Hierzu verwendet man Schleifmops mit Riemenantrieb, ein Prozess, den man "Soft-Form-Schleifung" nennt. Ein rotierender Schleifmop mit feinster Körnung tastet die Oberfläche des Furnierholzes ab, so dass die Bentley-Handwerker erkennen können, dass sogar die Einfassungen und Öffnungen für die Bedienelemente korrekt geschliffen sind, bevor das Furnier mit Polyurethan-Lack versehen wird.
Die Holzfurniere werden zunächst von einem Bentley-Fachmann in der Holzwerkstatt sorgfältig geprüft. Dazu wird ein Nassmop verwendet, um die Farbe des Furniers herauszuarbeiten. So wird jede Stelle mit kleinster Farbabweichung sichtbar, und das Furnier kann von Hand nachbearbeitet werden, bevor es mit PU-Lack in einem staubfreien Lackierraum versiegelt wird. Das Auftragen des Lacks ist eine der wenigen Aufgaben in Crewe, für die Roboter eingesetzt werden. Die Furniere werden durch einen Strichcode identifiziert, so dass der Sprüharm des Roboters den Code per Laser ablesen kann, die Komponente erkennt und ihrer Form genau folgen kann. Der überschüssige Sprühlack wird in einem 225 000 Liter großen Wasserbehälter aufgefangen. Darin wird der Lack so wirksam ausgefiltert, dass das Wasser nur zweimal im Jahr erneuert werden muss. Grundsätzlich wird das Wasser wieder aufbereitet, so dass es sich permanent wiederverwenden lässt.
Die lackierten Furnierhölzer müssen mindestens 72 Stunden ruhen, bevor sie abschließend bearbeitet werden. Dann wird das Furnierblatt an den Rändern auf seine endgültige Größe zurechtgeschnitten. Auch hier sorgt die in Crewe übliche Liebe zum Detail dafür, dass die Ränder der Trägerschicht so lackiert werden, dass sie genau mit der Farbe des Furnierholzes übereinstimmen.
Insgesamt sind zwischen 16,5 und 18,5 Arbeitsstunden erforderlich, um einen kompletten Satz von 15 verschiedenen Furnierblenden für jeden Continental GT herzustellen. Bei der vorangegangenen Generation, der in Crewe gebauten Autos, dauerte die Herstellung der Holzausstattung noch ganze 58 Stunden. Holz ist jedoch ein natürliches Material und man kann es nicht zur Eile antreiben: Berücksichtigt man die Zeit, die nötig ist, damit das Furnierholz seine Feuchtigkeit verliert, und die 72 Stunden, in denen der Lack härten muss, so dauert die Fertigung eines vollständigen Satzes von Furnierblättern für den Continental GT insgesamt zehn bis zwölf Tage. Damit ist die Holzverkleidung die Unterbaugruppe mit der längsten Herstellungszeit im gesamten Werk.
Leder und Innenausstattung: Traditionelle Bentley Fähigkeiten, menschliche Erfahrung und lasergenaue Ausführung.
Der Charakter eines Bentley wird auch durch seine besondere Innenausstattung bestimmt. Ganz wesentlichen Anteil am Gesamteindruck haben die handgenähten Lederbezüge auf allen Oberflächen, die den Tast- und Geruchssinn ansprechen. Sie werden aus feinstem Leder angefertigt. Aber auch die beste Qualität birgt winzige Fehler und kleinere Unzulänglichkeiten, und daher trägt die Erfahrung und das Urteilsvermögen der Männer und Frauen in der Lederwerkstatt von Crewe wesentlich dazu bei, dass jeder Satz von Lederbezügen so gleichmäßig und weich wie irgend möglich ist.
Früher wurden in Crewe die einzelnen Stücke aus der vollständigen Lederhaut mit Pressen und Schneideformen ausgeschnitten, die von Hand angesetzt wurden, um das Material möglichst effizient zu verwenden. Heute dagegen wird das Leder mit einem computergesteuerten Laser zugeschnitten. Das menschliche Urteilsvermögen ist aber immer noch wesentlich für den Herstellungsprozess: Die Handwerker und Handwerkerinnen kleben Leuchtband auf die Stellen des Leders, die kleine Fehler oder Unzulänglichkeiten in der Maserung haben, und das Laserschneidegerät errechnet dann automatisch die optimale Nutzung des Leders, um die Stücke in den verschiedenen Formen und Größen herauszuschneiden und dabei die markierten Stellen zu vermeiden.
Im Vergleich zum früheren System, bei dem 15 Häute nötig waren, um einen Satz Lederbezüge für einen Wagen herzustellen, ist es mit der neuen Technologie jetzt möglich, die Bezüge für den Continental GT in der selben Qualität aus nur 11 Häuten zu fertigen
Die kompletten Lederbezüge werden immer noch auf traditionelle Weise auf Nähmaschinen hergestellt, und einige der kniffeligsten Stellen der Lederpolsterung werden nach wie von Hand angefertigt. So wird beispielsweise die makellose Ledereinkleidung des Lenkrades von Hand mit Doppelstichen genäht, wobei mit zwei Nadeln gleichzeitig gearbeitet wird. Die Handwerker und Handwerkerinnen, die diese Aufgabe erfüllen, haben ihre eigenen, speziell eingerichteten Arbeitsplätze für diese genau und exakt auszuführende Tätigkeit.
Der Continental GT wird fertiggestellt
Wenn der Wagen wieder auf dem Montageband ist, werden Unterbaugruppen wie Sitze, Armaturenbretter, Innenausstattung und Türen am Montageband bereitgestellt. Dies ist ein weiterer Aspekt des neu gestalteten Werkes, der dazu beiträgt, die Kommunikationswege kurz und effektiv zu halten: In der gesamten Monatagehalle sind beleuchtete Schilderbrücken angebracht, die den Managern der Linien eventuelle Problembereiche sofort anzeigen. Jeder Mitarbeiter, der am Montageband arbeitet, kann den Prozess stoppen, indem er eine Leine an seinem Arbeitsplatz zieht. Dies wird automatisch auf den Tafeln angezeigt, so dass genau bestimmt werden kann, wo die Verzögerung eingetreten ist. Aber auch die Elektrowerkzeuge sind mit einem programmierten Benachrichtigungssystem versehen. Wenn zum Beispiel der (unwahrscheinliche) Fall eintritt, dass ein Bolzen Metallspäne in seinem Gewinde hat, kann die elektrische Werkzeugmaschine den Verschluss nicht bis zum richtigen Drehmoment anziehen, und diese Information führt automatisch dazu, dass die Produktion angehalten wird. So ist sichergestellt, dass der fragliche Bentley so lange stehen bleibt, bis jede Schraube perfekt angezogen ist.
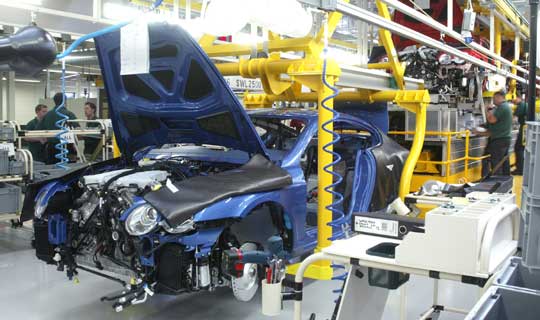
Nicht nur eine Reihe automatischer Kontrollen gewährleistet eine hohe Fertigungs-qualität, sondern vor allem ein Arbeitsethos, dem der Anspruch zugrunde liegt, dass jeder Handgriff von vorn herein perfekt sitzt und jeder Einzelne dabei auch auf die Arbeit achtet, die der Kollege an der vorhergehenden Station ausführt. Jeder im Team kann sich auf den anderen verlassen.
In der Nähe des Bandes befindet sich der Qualitätsbereich mit einer Continental GT-Karosserie aus massivem Aluminium in den Originalabmessungen des Autos. Mit dieser Funktionsprüfanlage in voller Größe, CUBE genannt, können alle Fragen des Einpassens und der Kompatibilität von Komponenten oder Unterbaugruppen am Original geprüft und Fehlerursachen schnell identifiziert werden.
Abschließende Arbeiten
Wenn der Continental GT sich dem Ende des Montagelinie nähert, passiert er eine rheostatisch gesteuerte Lichtkabine - auch dies ist ein Standardtest der Volkswagenkonzerns - in welcher Karosserie und Lackierung unter perfekten Lichtverhältnissen kontrolliert werden. Danach wird der Continental GT durch eine Hydropulsanlage gefahren, in der eine "sportliche" Fahrt über eine holprige Straße simuliert wird und Federung und wie Fahrwerk sich auf ihre normale Fahrhöhe einspielen können.
Hat das Fahrwerk seinen normalen Straßenzustand erreicht, fährt der Continental GT auf einen Rollenprüfstand, wo Spur ( Radnachlauf ) und Sturz der Räder mit Hilfe von Laserstrahlen geprüft und eingestellt werden. Erst dann werden die vorderen Scheinwerfer mit Hilfe des automatischen Einstellungssystems von Visicon eingestellt. Zuvor muss überprüft werden, ob Fahrgestell und die Fahrhöhe in jeder Hinsicht den vorgegebenen Spezifikationen entsprechen.
Von hier aus fährt der Continental GT auf einen weiteren Prüfstand, wo er mindestens 12 Minuten lang mit unterschiedlichen Geschwindigkeiten gefahren wird, um alle Funktionen zu überprüfen und um die Akustik zu messen. Der Continental GT wird nun über eine Teststrecke gefahren, um Klapper - und Quietschgeräusche festzustellen. Anschließend muss er den "Monsun-Test" bestehen: Hier prasseln volle 17 Minuten lang Wassermassen auf ihn nieder, die gewaltiger sind als ein tropischer Gewittersturm, und kein einziger Tropfen darf in den Innenraum eindringen. Jeder Continental GT wird geprüft und probegefahren. Erst dann hat er den Kontrollpunkt 8 passiert, den Schlusspunkt in der Reise durch die Produktion, bevor er in die Verantwortung der Verkaufsabteilung übergeht und den Weg zu einer der 140 Bentley-Händlern in der Welt antritt.
Werk-Logistik und die Schlüsselrolle der Zulieferer
Das Engagement für den Continental GT und die angestrebten gesteigerten Produktionsvolumen erstreckt sich auf alle Bereiche des Werks. Bis zu 100 Lastzüge pro Tag werden für die erforderlichen Just-in-time-Lieferungen mit dem Ziel einer Lean Production notwendig sein. Daher ist der Verkehrsfluss von entscheidender Bedeutung, und durch die Erschließung von bisher nicht genutzten Bereichen des Werks ließ sich 15 % mehr Platz gewinnen, um die Zulieferungen über zwei Entladebereiche regensicher und reibungslos abwickeln zu können.
In Crewe wird ein Vorrat an Rohkarosserien für bis zu drei Tagen vor Ort lagern, die bereits lackiert aus dem Volkswagen-Werk in Mosel (Sachsen) kommen. Die lackierten Rohkarosserien werden auf einem automatisiertem Hochregallager aufbewahrt, von wo aus sie entsprechend in der programmierten Reihenfolge auf die Reise zu der Montagelinie transportiert werden.
Von den anderen Komponenten wird in Crewe nur ein Vorrat für jeweils einen Tag bzw. zwei Schichten gelagert. Somit ist der reibungslose Fluss von Komponenten in die Produktionslinie - das KANBAN-System - ein Schlüsselelement bei der Fertigung des neuen Continental GT. An den Montagelinien wird ein Pool von Transportwagen unterwegs sein, um die Komponenten-Behälter ständig nachzufüllen.
Die Transportverpackung von Komponenten und Unterbaugruppen stellt in vieler Hinsicht eine Herausforderung dar. Die Verpackung zu entfernen und zu komprimieren kostet Zeit, Geld und Raum, aber ein Entsorgen wäre ebenso kostenintensiv und würde die Umwelt belasten. Bentley Motors hat das Problem durch die Entwicklung von äußerst widerstandsfähigen, wiederverwendbaren Kisten und Verpackungen, die allen Zulieferern zur Verfügung gestellt werden, gelöst. Wenn ein Lkw mit einer neuen Lieferung von Komponenten eintrifft, wird er nach dem Entladen mit den leeren Verpackungen des Vortags aufgefüllt, die erneut verwendet werden können.
Sauberkeit und Liebe zum Detail - eine Bentley Priorität
Eines der ersten Dinge, die der Besucher bemerkt, wenn er die Montagebereiche betritt, ist die Sauberkeit im Werk, die sich bis auf das kleinste Detail erstreckt. Die Müllsäcke sind aus durchsichtigem Kunststoff, so dass die Teamchefs und Manager mit einem Blick feststellen können, ob Abfälle am richtigen Platz gelandet sind. Die Schränke haben Glasvorderseiten, so dass ihr Inhalt sichtbar ist - das Ziel besteht darin, jegliche Unordnung zu vermeiden. Rund 1, 1 Million Euro wurden für den Fußboden ausgegeben. Er hat eine metallisierte Acrylbeschichtung, die für den Gebrauch in Krankenhäusern und Laboren entwickelt wurde und am Ende jeder Doppelschicht absolut blank poliert werden kann. An jedem Arbeitsplatz sind Halterungen für Handfeger und Schaufel angebraucht, und jede Arbeitsgruppe ist verpflichtet, Abfall in ihrem Bereich vollständig zu entfernen. Werkzeugkästen, Komponenten-Behälter, Schränke und Arbeitsbänke stehen auf großen, gummibereiften Laufrollen, so dass die gesamte Fertigungslinie einmal am Tag zur Säuberung freigeräumt werden kann.
Die Mitarbeiter in Crewe - das größte Kapital von Bentley Motors
Bei der Planung der neuen Produktionsanlagen für den Continental GT wurde größter Wert auf die Erhaltung des besonderen Charakters und der Individualität eines Bentleys gelegt, die in großem Maße von den Menschen abhängen, die ihn planen, entwickeln und bauen.
Obwohl das Produktionsvolumen gravierend gestiegen ist, dient die Automatisierung in der gesamten Fertigung des Continental GT ausschließlich als Hilfsmittel, um höhere Qualitätsstufen zu erreichen, keinesfalls vermindert dadurch aber die Bewertung menschlicher Fähigkeiten. Es gibt nur zwei Bereiche im Produktionsablauf des Continental GT, bei denen Menschen durch Roboter ersetzt werden: Die Lackbeschichtung der Holzpaneele, weil hier wegen der gewünschten Gleichmäßigkeit der Lackierung sowie aus Gesundheits- und Sicherheitsaspekten die Maschine eine sinnvolle Alternative darstellt; und der automatisierte Kleberauftrag auf die Ränder der Fenster- und Windschutzscheibenöffnungen der Karosserie, eine monotone Aufgabe, bei der es erforderlich ist, die Beschichtung in einer absolut gleichmäßigen Linie aufzutragen und den Zerstäuber gleichmäßig zu führen. Abgesehen von diesen beiden Bereichen wird jeder Montagevorgang von erfahrenen Männern und Frauen im Werk in Crewe geleitet und überwacht.
Ganz anders als in der Vergangenheit gehört zu jedem Arbeitsbereich ein Erholungsbereich in der Nähe der Montagelinie, in welchem die Mitarbeiter ihre Tee- und Mittagspausen einlegen und sich entspannen können. Jeder Bereich hat bequeme Sitzgelegenheiten, einen Kühlschrank und einen Mikrowellenherd, so dass die Mitarbeiter keine weiten Wege zurücklegen müssen, wenn ihre Pause beginnt.
Crewe hat für die Herstellung des Continental GT seinen Personalbestand erweitert. Die Zahl der in der Fertigung beschäftigten Mitarbeiter beträgt jetzt 1200. Bevor ein neue(r) Mitarbeiter(in) in der Herstellung eines Bentley mitarbeiten kann, absolviert er oder sie einen fünfwöchigen Kurs, der aus Unterricht und praktischem Training besteht. Bei Bentley fühlt man sich den einzigartigen Standards und Arbeitsweisen verpflichtet und daher wird kein standardisiertes Unterrichtsprogramm "eingekauft", sondern aus den Reihen der Produktionsmitarbeiter heraus ein spezielles Trainingsprogramm entwickelt.
Wenn neue Mitarbeiter in Crewe anfangen, werden sie den einzelnen Arbeitsgruppen zugeordnet, von denen jede einen eigenen Teamchef hat. Dabei beträgt das Verhältnis von Teamchefs zu Mitarbeitern 1:6, und der Teamchef eines jeden Bereichs verfügt über die Qualifikation, jede Aufgabe innerhalb dieser Gruppe auszuführen.
In täglichen Lagebesprechungen vor Beginn jeder Schicht werden mögliche Probleme besprochen, die - sofern der Teamchef sie nicht selbst lösen kann - an höhere Stellen weitergeleitet werden. Somit werden mögliche Engpässe schnell identifiziert. Darüber hinaus kann jeder Mitarbeiter Vorschläge zur Verbesserung der Qualität und/oder der Produktivität machen und seine eigenen Arbeitsmuster entwickeln. Die Arbeit der Mitarbeiter wird auch auf Video aufgezeichnet, so dass das Team mit Hilfe dieser Filme feststellen kann, in welchen Bereichen Verbesserungsmöglichkeiten bestehen.
Ein neues Werk in Crewe - eine neue Generation von handgefertigten Bentleys.
Im Vergleich zu den begehrten Bentley Arnage R und Arnage T, deren Fertigung im Schnitt 500 Arbeitsstunden erforderten, wird jeder Continental GT, der das Werk verlässt, in 250 Arbeitsstunden gebaut worden sein. Aber es lohnt sicht, diese Zahlen in einen Kontext zu stellen. Durchschnittliche Mittelklassewagen werden nämlich in nur 20 bis 30 Arbeitsstunden komplett zusammengesetzt.
Der Continental GT ist deswegen ein wirklich individuelles und handgefertigtes Automobil, bei dem die Leistung, die Qualität des Materials und das Design einen einzigartigen Wert in seiner Preisklasse darstellen. Darüber hinaus werden gerade die Faktoren, die den Besitz eines Bentleys zu einem so einzigartigen Erlebnis machen - das Gefühl, dass Sie ein von Hand gefertigtes Hochleistungsfahrzeug fahren, das nach Ihren individuellen Vorstellungen und Angaben ausgestattet ist - durch die menschliche und finanzielle Investition, die in Crewe getätigt wurde, bewahrt und geschützt.
Das Werk in Crewe zu besuchen und zu sehen, wie ein Bentley hergestellt wird, offenbart eines der Wunder der Automobilwelt. Mit der Einrichtung der Produktionsanlage für den Continental GT wurde sichergestellt, dass diese Erfahrung einer neuen Generation von Bentley-Fahrern vermittelt wird, die das Gefühl eines großen persönlichen Engagements zu schätzen wissen, wie es nur in einem Werk wie das in Crewe und durch seine Mitarbeiter möglich ist.
Text &Fotos: Bentley